Since its development in the late 1970s, the Just-in-Time (JIT) model for supplying manufacturers and retailers has come to dominate global demand forecasting and supply chain management. By cutting down the active supply of goods and parts to a small window through digital management, the Japanese carmaker Toyota pioneered a method that all but eliminated sprawling stockrooms and unintentional wastage. Parts arrived at the worker or robot, who added it to each car ‘just in time’ – creating a seamless, fast assembly line and supply chain. Demand forecasting, direct ordering, globalisation, and active data monitoring enhanced JIT further, creating intricate global supply chains to meet demand at the lowest possible cost to companies.

A More Fragile World
Before 2020, major UK supermarkets, factories, and online retailers all relied heavily on JIT to maximise profits and keep supply chains moving. However, the chaos caused by lockdowns and travel restrictions reveals the fragility of the model, and now permanently threatens JIT’s place at the head of the table.
Shock ‘black swan’ events in Q1-Q2 2020 resulted in mass global shortages of vital products (such as PPE, toilet paper, and hand sanitiser), price spikes, and public panic as ageing JIT systems struggled to cope or outright collapsed. While most retailers have now recovered in Q3 2020, many are still suffering from restricted product lines, overproduction pile-ups, and lost profits due to JIT outages and failures. Why did this happen?
Risky Business
The global shift towards JIT really began in the late 1990s, a time of exceptional economic and political stability in the West. The JIT shift coincided with the mass expansion and outsourcing of base manufacturing to China. Companies jumped at the chance to adopt a method that streamlined both profits and productivity. A scenario of complete global disruption seemed impossible.
Manufacturers and providers responded to JIT’s precision control of sourcing by becoming hyper-specialised and adopting JIT themselves in an increasingly competitive, restricted marketplace. Older safeguards such as redundant manufacturing machinery, local suppliers, and source diversification fell by the wayside. Too many companies assumed that their world would stay the same way – forever.
When the pandemic emerged in Wuhan, China in January 2020, the house of cards collapsed. Business analysts were quick to point out the extent to which previously resilient ‘cushioning’ had been sacrificed over 40 years for the sake of marginal efficiency, more money, and (at the time) shiny new technology. JIT’s future as a popular supply chain management method is now in serious doubt.
Back To Normality?
What happens next? It all depends on how quickly businesses learn the lessons of 2020 and integrate this knowledge into their supply chain management and forecasting models – and how responsive their systems are to change.
While JIT still has a long-term part to play in manufacturing, uses may be more limited in the near future, with the renewed popularity of on-shoring to replace strung out supply chains. One solution mooted is the mass adoption of Just-in-Case (JIC) – an alternate model that aims to strike a fair balance between contingency stockpiling and costly overstocking. JIC has assisted in areas with unreliable infrastructure, high-risk transport, and active natural disasters (such as floods).
JIC uses disaster planning, risk mitigation funds, and demand forecasting software to create warehoused backups and alternative routes where needed. Planning exercises and crisis drills are also adopted, adding staff resilience to unexpected problems. JIC also focuses heavily on the benefits of localisation – onshoring production facilities and shortening freight trips may be far less costly in the years to come. Finding a careful balance between risk and profit by using the best software and data monitoring available will be key to navigating the world through the Covid recovery and into better times.
Demand Forecasting With Reflex Planning
The unexpected is just that – unexpected. The best defence against circumstances beyond your control is responsive and accurate forecasting and supply chain management. With demand projection software from Reflex, you can protect your supply chains against shortages and overstocking by creating a flexible, resilient model of supply that anticipates hazards and opportunities alike. Call us today to arrange a free product demo and to learn more about what we could do for you.
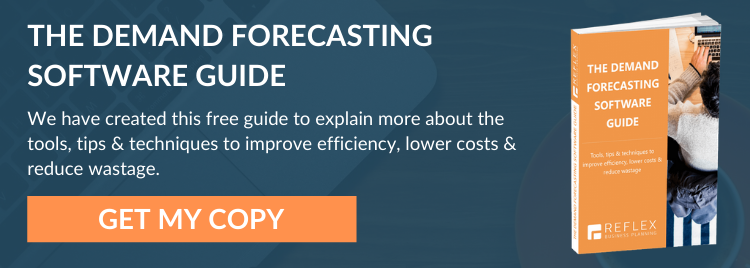
Image source: Pixabay